Introduction
Welding is a fundamental process in fabrication and construction, joining metals together to create strong and durable structures. However, choosing the right type of welder for your project can be daunting, especially with the variety of options available in the market today. In this guide, we’ll explore the different types of welders and help you determine which one suits your needs best.
Understanding Types of Welders
There are several types of welders, each with its own unique characteristics and applications. Let’s take a closer look at the most common ones:
Stick Welders (SMAW)
- Stick welders, also known as Shielded Metal Arc Welders (SMAW), are one of the oldest and most versatile types of welders. They use a consumable electrode coated in flux to create the weld. Stick welders are suitable for welding thick metals and are ideal for outdoor welding or in situations where portability is essential.
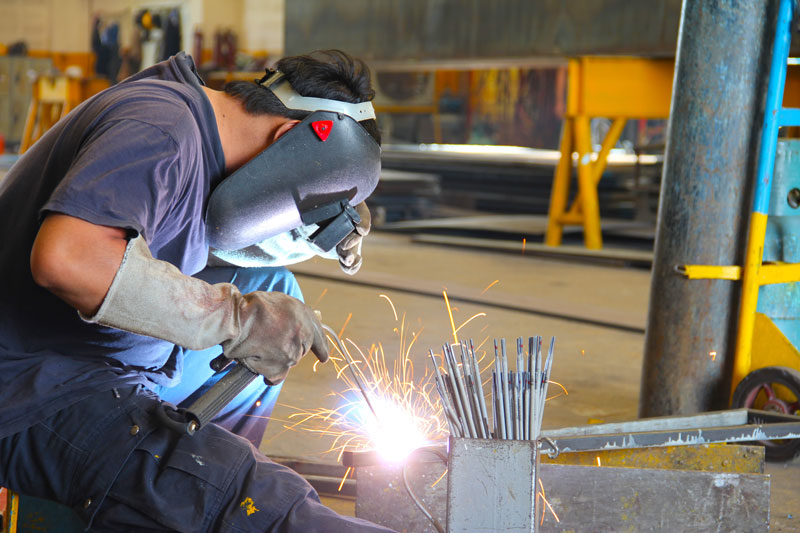
MIG Welders (GMAW)
- MIG welders, or Gas Metal Arc Welders (GMAW), utilize a wire electrode fed through a welding gun, along with a shielding gas, typically a mix of argon and carbon dioxide. MIG welding is known for its ease of use, high welding speed, and clean welds. It’s suitable for welding thin to medium-thickness metals and is commonly used in automotive, construction, and fabrication industries.
TIG Welders (GTAW)
- TIG welders, or Gas Tungsten Arc Welders (GTAW), produce welds using a non-consumable tungsten electrode and a separate filler material if needed. TIG welding offers precise control over the welding process, making it ideal for intricate welding projects, thin metals, and applications where aesthetics are crucial, such as stainless steel or aluminum fabrication.
Flux-Cored Arc Welders (FCAW)
- Flux-Cored Arc Welders (FCAW) are similar to MIG welders but use a tubular wire filled with flux instead of a solid wire electrode. FCAW is known for its high deposition rates and excellent penetration, making it suitable for welding thick materials and in outdoor or windy conditions where shielding gas may be ineffective.
Submerged Arc Welding (SAW)
- Submerged arc welding (SAW) is a high-productivity welding process that involves feeding a continuous wire electrode under a blanket of granular flux. The arc is completely submerged beneath the flux, resulting in high-quality welds with minimal spatter. SAW is commonly used in heavy fabrication, such as pressure vessel and pipeline construction.
Choosing the Right Welder for Your Project
Now that we’ve covered the main types of welders let’s discuss how to choose the right one for your project:
- Consider the thickness of the materials you’ll be welding. Stick welders are suitable for thicker metals, while MIG and TIG welders are better for thinner materials.
- Evaluate the welding environment. For outdoor or windy conditions, a flux-cored welder might be more appropriate.
- Think about your skill level and the complexity of the project. TIG welding requires more skill and precision compared to MIG or stick welding.
- Consider the power source available. Some welders require electricity, while others, like stick welders, can operate on generators or engine-driven welders.
In summary, choosing the right welder depends on factors like material thickness, welding environment, required weld quality, and personal preference. By understanding these factors and the different types of welders available, you can ensure the success of your projects, whether you’re a hobbyist, DIY enthusiast, or professional welder. Take your time to consider your options carefully before starting your next welding endeavor. Happy welding!
Conclusion
Choosing the right type of welder is essential for achieving successful welds and completing your projects efficiently. By understanding the different types of welders and their applications, you can make an informed decision based on your project requirements, skill level, and welding environment. Whether you opt for a stick welder, MIG welder, TIG welder, or flux-cored welder, each type offers unique advantages that can help you tackle various welding tasks with confidence and precision.
Comments 1